Over the past few decades, companies have adopted lean manufacturing principles to optimize various aspects of their operations. While lean methods are now ingrained in the DNA of most modern-day businesses, they can no longer depend solely on conventional lean tools to achieve continuous improvements to their processes due to the law of diminishing returns. This is why many companies are now looking towards industrial IoT platforms.
To remain competitive in the market, companies must look to disruptive new technologies to stay relevant. The most promising of these disruptions, Industrial IoT platforms or “digitally enabled lean”, help organizations reimagine their manufacturing operations by providing AI-enabled data-driven recommendations.
The benefits gained by leveraging Industrial IoT platforms outweigh those that can be attained through the first principles of operations management.
According to a study carried out by Accenture, by 2030, capital investments in the IIoT and the productivity gains that should follow are expected to add US$6.1 trillion to the United States’ cumulative GDP..Industries are aware of this, and adoption has begun at all levels. They’ve understood that soon, the question will become ‘What’s your IIoT strategy?’ from ‘Are you thinking of adopting?’. Now the question of choosing the right IIoT platform arises. One would notice a huge amount of platforms available, each catering to different aspects of IIoT. Generally, most of these offerings use generic predictive maintenance algorithms.
Here’s how our offering, Factory360 differs from the rest. Factory 360 helps our customers unleash the true power of Industry 4.0 by leveraging highly customized AI solutions that are designed to solve problems that are specific to our customers’ industry needs.
Manufacturers can leverage the power of our Machine Learning and AI models and connected devices in our Factory 360 platform to help them with business insights, predictive analytics, and prescriptive analytics. We have highlighted a few samples below:
1. Reduce Outages and Maintenance time
As the single largest source of productivity loss, asset downtime is often a critical challenge for manufacturers. Moreover, while numerous factors can lead to downtime, unplanned equipment failures and breakdowns are the primary contributing factors.
While generic predictive monitoring solutions measure tangible variables such as Temperature, Vibrations and Energy Consumptions; Factory 360 goes the extra mile and factors in highly specialized, intangible variables such as the profile of the equipment operator, unique attributes of the equipment, etc. to reduce downtime and help our customers consistently hit their production targets.
Our IIoT platform also helps our customers optimize their maintenance strategy by prescribing actionable insights derived by monitoring key metrics that measure maintenance activities such as the average Work Order Service Time, Open Service Requests and Schedule Compliance.
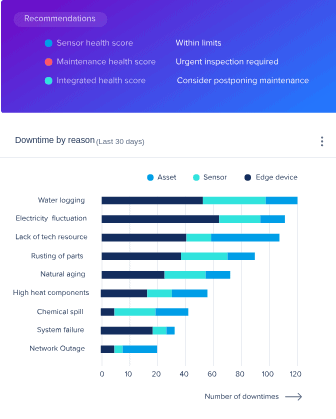
2. Improve Asset Performance
Factory 360 helps our customers bolster Overall Equipment Effectiveness (OEE), by holistically measuring their assets across myriad dimensions such as Quality, Efficiency, Performance, Reliability etc.We help our customers transform their approach to asset governance by optimizing maintenance and replacement actions based on the current health of the assets. The Factory 360 platform allows our customers to monitor factors such as condition, cost, performance, and the remaining useful life of their assets to define asset health and prioritize areas of focus.
To keep our customers’ businesses flowing, Factory 360 helps drive the efficiency of their maintenance process by improving metrics such as the first-time fix rate, mean time to repair, etc. by improving the efficiency of every maintenance technician. Our platform provides specific repair recommendations for even the most complex equipment to achieve Maintenance 4.0.
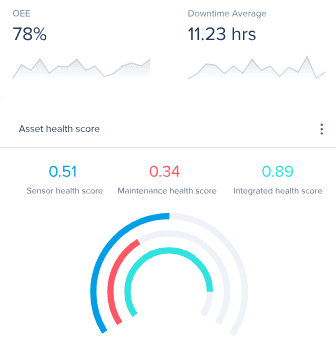
3. Improve Operational Efficiency
Factory 360 helps our customers improve every aspect of their operations: from sourcing through manufacturing to selling by improving the tracking and sensing capabilities of their supply and assembly chains. The insights gained from the gathered data help unlock efficiencies across areas such as forecasting, sourcing, task scheduling, replenishment, order management, and fulfillment.
One of our manufacturing customers employs our IIoT platform to power their scheduling system for their high-mix, make-to-order production operation. Our Data Lake aggregates customer order data and operational data from a multitude of enterprise databases, sensors, etc. Using this aggregated and cleansed data, our AI/ML models were able to predict and avoid bottlenecks in their Job Shop.
Our platform helped the customer garner insights from metrics such as Idle Time, Capacity Utilization, Engineering Change Order Cycle Time etc. to reduce their lead time by 50% thus improving both productivity and the flexibility of the plant.
4. Improve Quality and Reduce Waste
Factory 360 uses techniques such as image recognition, condition monitoring, control charts, and so on to catch quality slippages before they happen. The quality monitoring workflow in our platform brings the power of AI to the traditional Plan-Do-Check-Act cycle to help you build a leaner production line. Our customers use our smart scheduling algorithms to reduce the testing time by creating batches of similar finished goods, thus reducing the test setup time.One of our customers used image analytics of their assembly line to define standard operating procedures (SOP) and monitor their 5S standard for their manufacturing operation. The customer was able to detect deviations from the defined procedures using IoT devices coupled with Factory 360’s customized AI algorithms. This enabled the customer to develop processes that tightly coordinated man, machine, material, and method (the 4 M’s), which made possible the early identification and elimination of potential quality defects and improved overall quality.
The metrics provided include Yield, Variance, Customer rejects/returns, Quality of incoming material, Failed audits, etc.
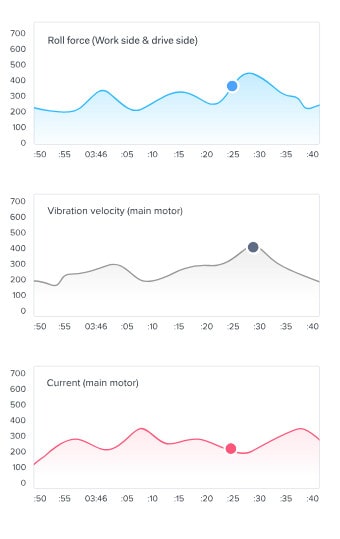
5. Improve Safety
According to the National Safety Council, employee injuries cost more than $250 billion each year, including $182 billion in lost wages and productivity.
Factory 360 enables you to collect IoT data from wearables (like helmets, jackets, and watches, for instance) and combine them with environmental sensors to monitor both workers’ wellbeing and the state of their working environment. By tracking vital parameters of physical fitness like heartbeat and skin temperature, sensors can help watch out for employees who are starting to show strain or other signs of potential problems, which would then allow preventative action to be taken.
Factory 360’s condition monitoring feature helps our customers monitor potential hazards within the working environment. For example, our IIoT platform allows you to define permissible thresholds for carbon monoxide levels, weather events, temperature, and vibration etc. Our algorithms ingest the data generated by the sensors monitoring these attributes and prescribe proactive actions to be taken to minimize the risks to the workers and reduce downtime from such incidents.
Factors 360 Enables Smart Industries
At it’s core, what we’re trying to do is give factories a suitable method to become more efficient. By both eliminating manual work (along with the errors associated with them) & adding layers of ML to the components for more effective equipment tracking. Our IIoT platform lets factories automate all of the grunt work, as well as get timely, algorithm-fueled insights that can make their factories run longer & produce more output.